Our offer
The Wiór-met company in the broadly understood scope of machining has been operating on the market since 1964, as a trusted supplier of parts that are used in various industries, including machinery, food, construction.
We are aware that in our industry precision is synonymous with quality, which is why the machines and devices we work on have all the required certificates. Based on the adopted procedures, we conduct systematic quality control of our products. In addition, all production processes are subject to constant supervision in terms of compliance with the requirements of the Quality and Environmental Management System.
We have the ability to process the following materials: steel, stainless steel, bronzes, copper, brass, various types of castings, aluminum, plastics, specialist materials and all kinds of novelties – according to the customer’s wishes and needs.
- Thanks to the qualified staff and market orientation, finding an unusual type of material is not a problem for us.
- Our employees have a very large theoretical knowledge, qualifications and skills, supported by many years of experience, high know-how, which they use on a daily basis in the execution of orders.
- Very good contacts with material suppliers enable us to execute contracts on time.
- All materials on which we work have the necessary approvals. After the details leave the production, they undergo a thorough quality control, after which a measurement report is attached, confirming compliance with the customer’s documentation.
Machining
It involves the removal of individual layers of the excess material and is divided into chipping and abrasive machining. Chip machining is performed with tools with a fixed geometry and number of teeth, and the resulting chips have a specific shape, depending to a greater or lesser extent on other factors such as the workpiece material, feed rate, cutting speed, cutting temperature, etc. Abrasive machining, on the other hand, is characterized by very fine blades with an indefinite number and geometry, with the product being chips in the form of small particles, also of undetermined geometry.
Lathework
A type of machining in which the workpiece rotates, driven by the lathe spindle, and the tool feeds. These movements overlap, add up and, in the end, achieve the previously planned goal of turning machining. This allows you to remove the outer or inner layer of the material and give it the desired shape. The surfaces of turned objects can be cylindrical or conical, i.e. rectilinear, and spherical, egg-shaped, etc. (curvilinear). Threads and worms are also turned. Using this method, we make, among others, pins, shafts, axles, bushings, piston rods and other elements that require precise grooves and recesses while maintaining specific surface parameters. During machining turning, there are forces that are divided into: cutting force, feed force and repulsive force.
The magnitudes of these component forces depend on each other. The magnitude of the component forces is influenced by the type of the machined material and its hardness and strength or the thickness of the machined layer. It also depends on the amount of feed, as well as on the geometric shape of the knife edge, especially on the angle of its entering and the rake angle.
- Ø 550 mm for short elements, length of elements:
3000 mm with a maximum diameter of Ø 250 mm - Thread types: metric, inch, trapezoidal, etc.
from 1 to 160 mm with a length of 1200 mm
CNC lathes allow us to significantly improve our machining and reduce the time needed to produce a specific item. Lathing on CNC machines is also much more precise and gives the possibility of serial production, as a result of which each item will have identical parameters.
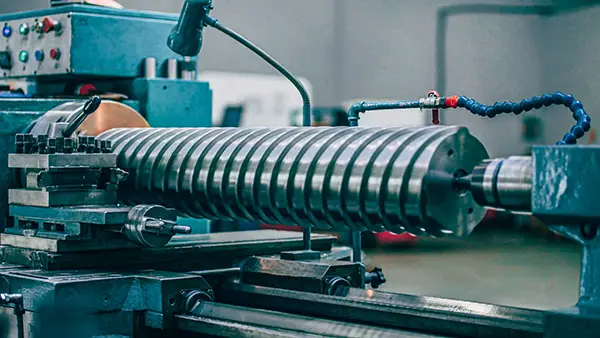
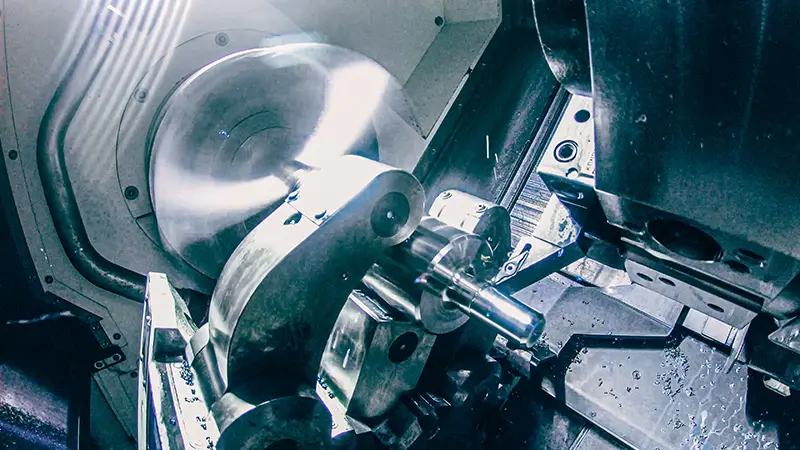
Milling
Milling is a type of machining in which the rotary movement is always performed by the tool, and the feed movement (depending on the construction of the machine tool on which the machining is carried out) is also performed by the tool or the workpiece. This is one of the most universal machining methods that allows you to make almost every detail. It consists in introducing rotation of a multi-edge tool – a milling cutter whose edges do not work simultaneously, but one after the other, while the workpiece performs a sliding movement. This method allows us, among other things, to machine surfaces, cut threads, make gears or grooves.
- Universal: vertical milling machine, horizontal milling machine, vertical-horizontal milling machine, slotting machine, drilling and milling machine. We mill surfaces: 400 x 900 mm
- CNC milling machine with the possibility of working space 1000 x 500 x 500 mm
Depending on the type of material to be machined and its hardness, we select appropriate cutting tools as well as milling parameters so that the final product meets all technical requirements. The concept of machinability is usually understood as a set of properties, features of the workpiece material that affect the course of the cutting process and the selection of the best cutting parameters. The machinability of steel varies depending on the composition of the alloy, the course of heat treatment and the production technology. When milling steel, we follow recommendations regarding, for example, setting the cutter in order to avoid the formation of thick chips at the exit of the blade from the material, and we consider the possibility of dry operation without the use of cutting fluid, especially during roughing.
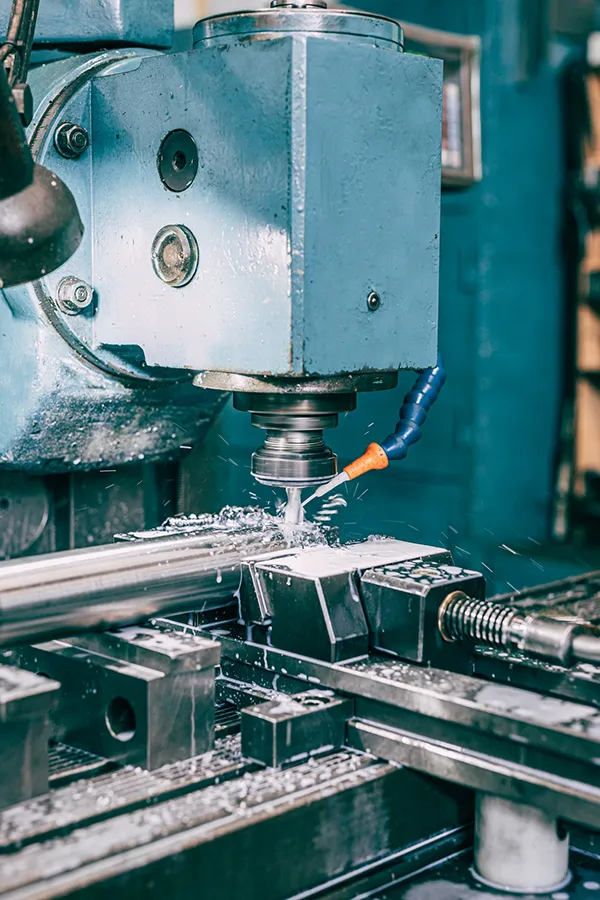
Grinding
Abrasive treatment used to finish an object and smooth its surface. We do it with grinding wheels, abrasive belts and abrasive material, which hook on the treated surface and cut a thin layer of material from it. In the grinding process, high dimensional accuracy of the element, stability of dimensional deviations and low roughness are obtained.
- We grind flat surfaces: 320 x 600 mm
- We grind diameters: Ø 250 x 1300 mm
Grinding is a necessary process when there is a need to remove the excess of the processed material. Grinding allows us to get rid of the rough surface and give a specific shape in accordance with the technical requirements of the product.
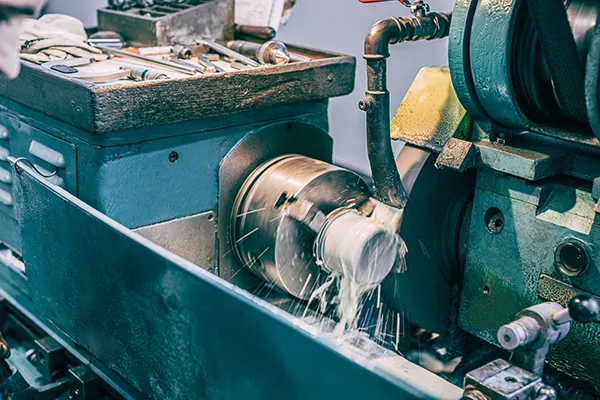
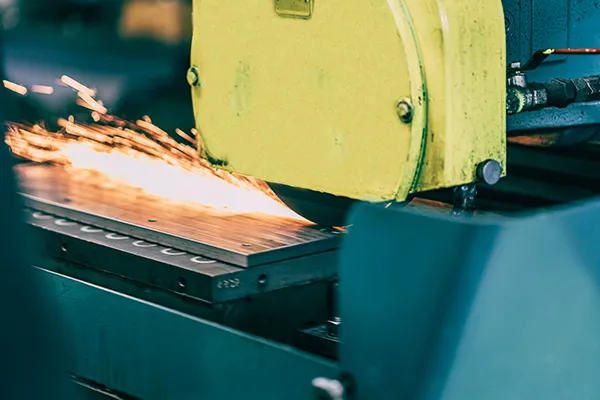
CNC Machining and Lathework
From small series to large series production.
A modern machine park, enriched with CNC machine tools, guarantees high precision and quality of details made by us. Computer-controlled numerical devices guarantee us a perfect representation of the assumed project, repeatability, maximum reduction of material consumption, and thus lower production costs. High shape and dimensional accuracy translates into no need for further processing and, thus, the entire process is faster and more environmentally friendly. The production of the parts is therefore automated. The measurement methods and control systems we use allow us to produce the highest quality elements.
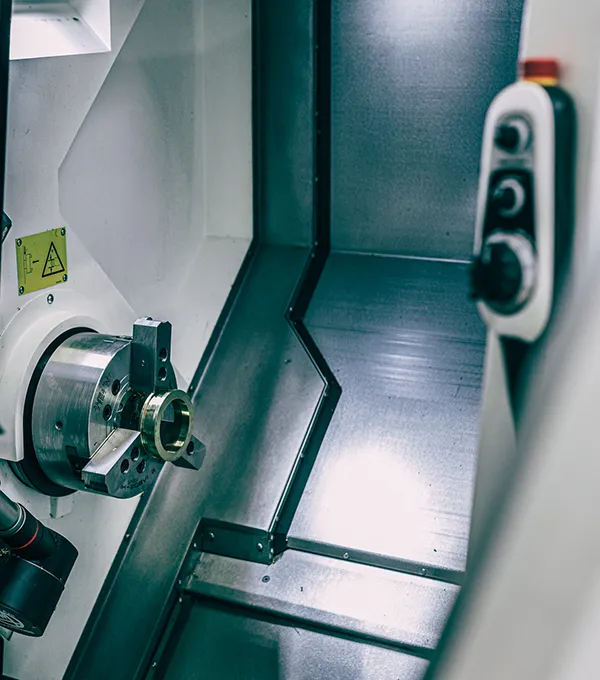
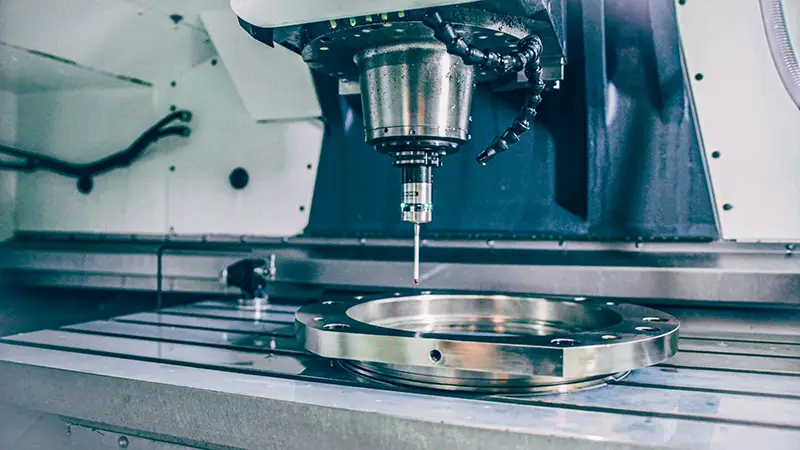
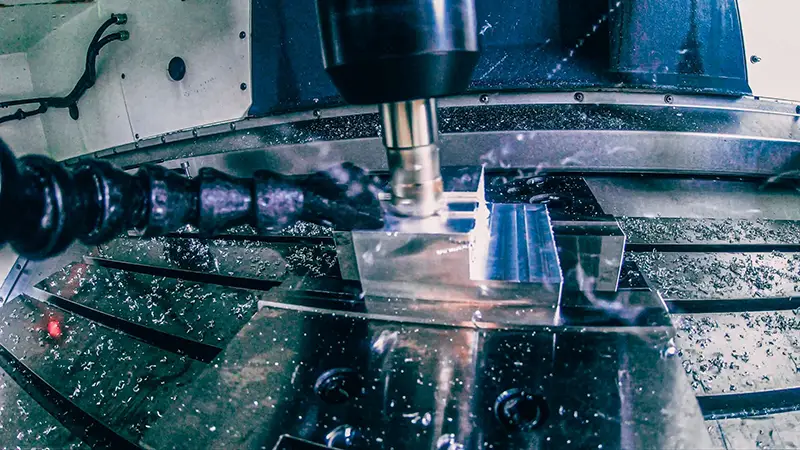
Application of chemical coatings
Satisfying the various needs of our customers, we met the expectations and in close cooperation with companies dealing with chemical processing, we can deliver the final product with various coatings. Cooperation in the field of comprehensive solutions applies to the application of chemical coatings in accordance with the customer’s documentation, including: chrome plating, nickel plating, zinc plating and painting. By adhering to rigorous quality control measures, we can guarantee excellent durability, corrosion protection and aesthetic appearance. Thanks to our advanced technology and a qualified team of professionals, we can provide custom solutions tailored to the unique needs of each client.

Thermal treatment
Providing our customers with products that meet specific hardness parameters is our priority. We cooperate with companies in the field of heat treatment services and provide details of appropriate hardness in accordance with the contractor’s requirements. Services include induction hardening, vacuum hardening, nitriding, carbonitriding and carburizing. Each of these techniques is carried out in such a way as to ensure the highest quality final product to meet the needs of many industries, including machinery, automotive and energy. Our commitment to quality and service ensures that our customers receive the highest quality products and services.
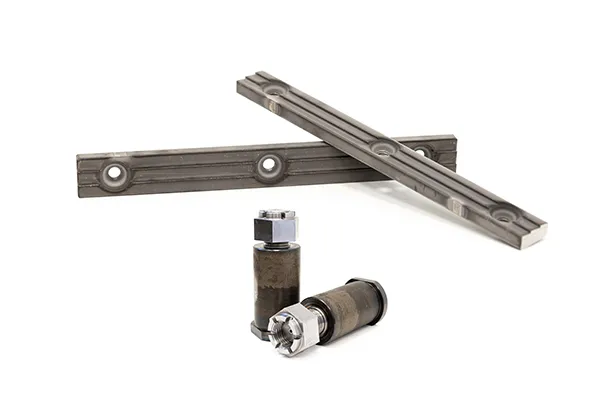
We take care of every detail
NOT ONLY IN PRODUCTION
By handing your order over to us, you provide yourself with comprehensive project support. We provide not only fast and timely order fulfillment, but also support at every stage, from professional advice, through the fabrication itself, to meticulous quality control. We work on the highest quality, certified materials, as well as on raw materials provided by the customer. Additionally, at the customer’s request, we attach the required certificates to each manufactured detail.

TRANSPORT
We take care of every aspect of order fulfillment, including transport. Ready, professionally packed products are delivered to the address indicated by the customer, maintaining all safety requirements. We are characterized by speed of implementation, reliability and punctuality.

QUALITY CONTROL
Although the machines used in our industry are becoming more and more precise, we assume that the quality control carried out at every stage is of key importance and is an irreplaceable process. The basis for maintaining the highest level of service is the consistent daily work of the entire team and high-class measuring devices, which, in order to obtain reliable results, are subject to periodic inspections and calibration.

ENGRAVING
To facilitate the identification of individual details, we provide a CNC engraving service on numerical machines. Our devices enable us to mark and cut in the hardest aluminum alloys and other metals.